STØTEK MEGA CASTING
![]()
|
Melting furnacesCentral melting |
![]() |
MEGA holding furnacesUp to 22,5 ton |
![]() |
Dosing/holding furnacesRadiant or immersion heated |
![]() |
Designed with focus onIncreased Safety |
SMG: Støtek Melting Furnace
Shaft furnace available in several sizes with a melting capacity up to 7 tons/hour.
The tapered shaft design gives optimum melting efficiency and the flat flame burners in the holding section ensures minimal metal oxidation.
Holding section with possibilities for metal alloying, degassing with porous plugs or lance, and treatment with impeller.
The melting speed is equal to the pouring speed. The holding section capacity is 2 - 2,5 times the ratio of the melting speed to ensure the highest possible metal quality Metal take-out through tap cone, tilting or ceramic transfer pumps with launder.
STET – STØTEK Mega Holding Furnace
- Up to 22,5 tons holding capacity
- Electrical heated with energy consumption approx. 50 kW/h (with 22,5 tons volume)
- Developed for keeping maintenance time and cost low
- Easy refilling of the furnace
- Hydraulic tilting for discharge of metal
STE, STI, DTE, DTI – STØTEK HOLDING AND DOSING FURNACES
- Heating with radiant heating in the top or directly in the metal with immersion heating elements.
- Holding furnaces for operation with open ladles.
- Dosing furnaces operated with ceramic dosing units and standard gravity dosing launders. Optional with Pro-Dose launders for dosing up-wards approx. 800 mm compared to standard gravity launder.
- Scissor jack for lifting and tilting.
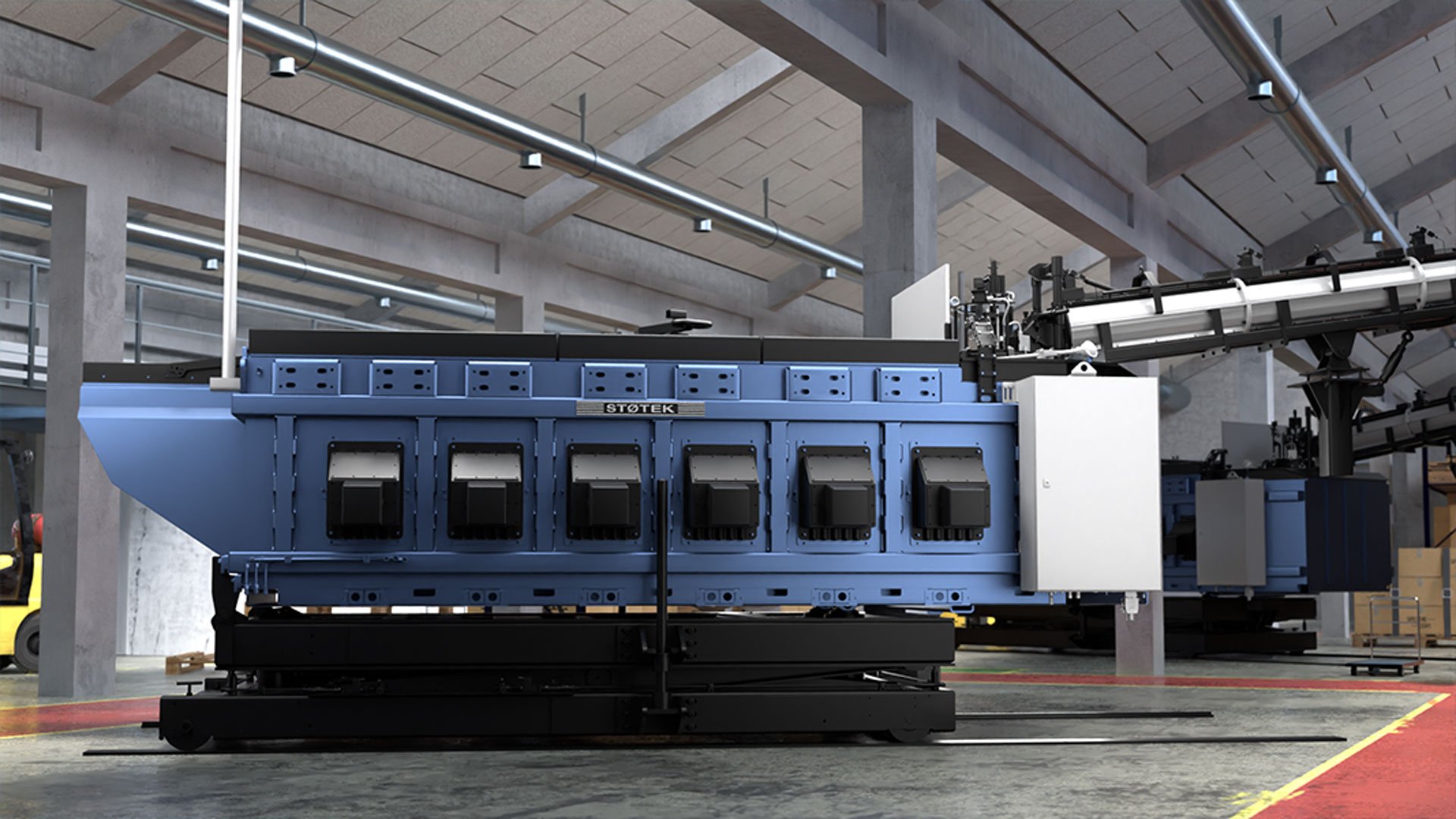
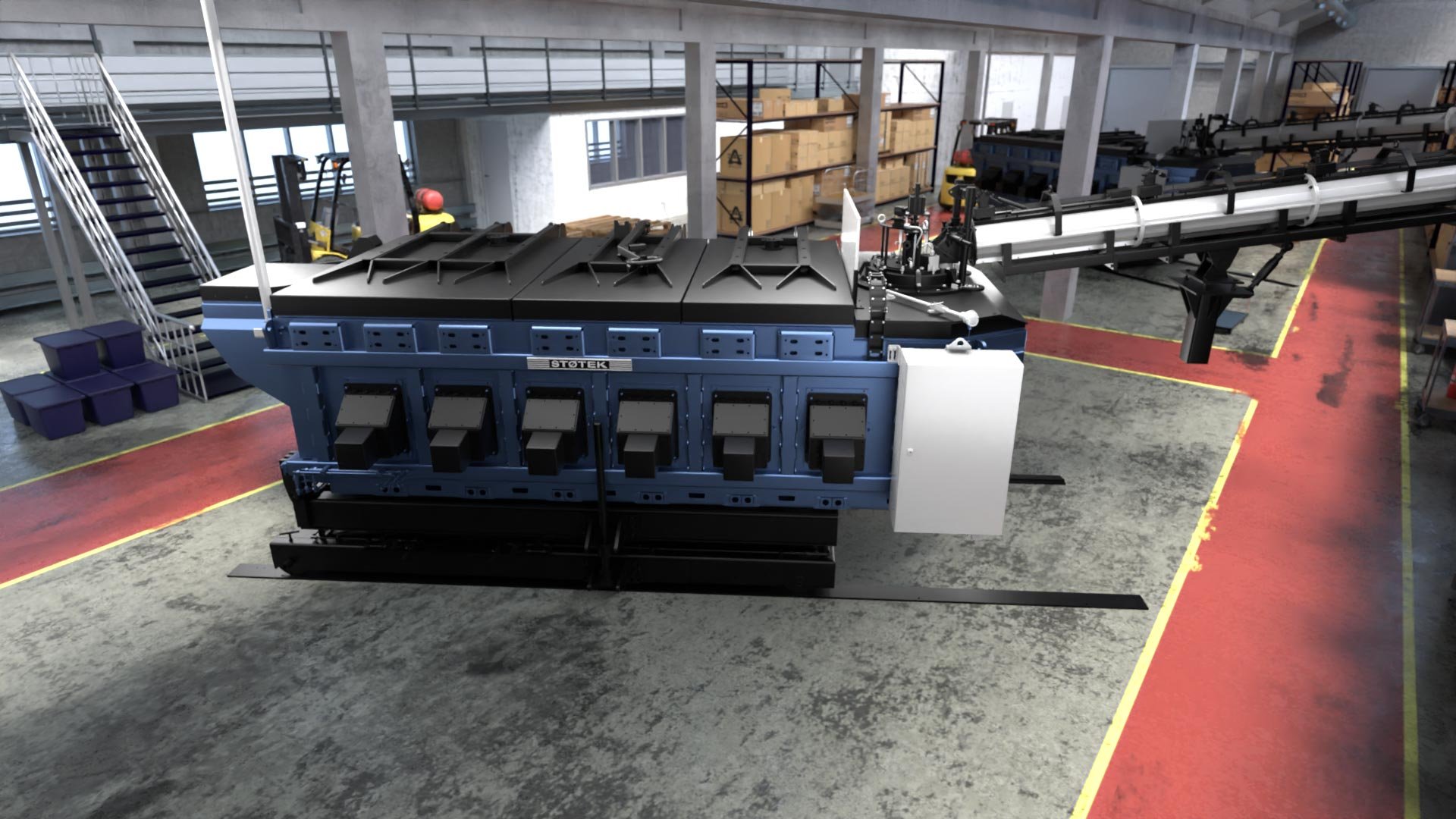
EXAMPLES OF CONFIGURATION
MELTING AT CELL
- SMG Shaft Furnace with 4 tons melting and 8 tons holding capacity
- Transfer of metal to dosing furnace with ceramic transfer pump and launder
- DTI6020 Dosing Furnace with 5 immersion heating elements and ceramic dosing unit
- Pro-Dose closed up-wards launder for dosing into shot sleeve
- Safety-focused design with lowest possible operating height for cleaning and maintenance.
CENTRALIZED MELTING
- Shaft furnace or large holding furnace
- Transfer with level-controlled transfer unit to launder system for distribution to holding or dosing furnaces.
- Alternatively, transport ladles can be used.
- DTI/DTE Dosing Furnaces or STI/STE Holding Furnaces at each casting cell.
Pro-dose technology
Improves productivity
- No lifting time when receiving dosing signal
- No drip time after dosing
- Dosing speed up to +10kg/s
- Up to 160kg dosing weight.
Improves Safety
- Filling height 500mm below shot sleeve
- No visible aluminium from filling funnel to shot sleeve
Improves metal quality
- Eliminates oxidation from furnace filling to shot sleeve
- Accurate temperature control all the way to shot sleeve
- Accurate dosing of ±1% by weight
Cleaning
- Dosing unit each week – 15 minutes
- Pro-Dose tube each 8 weeks